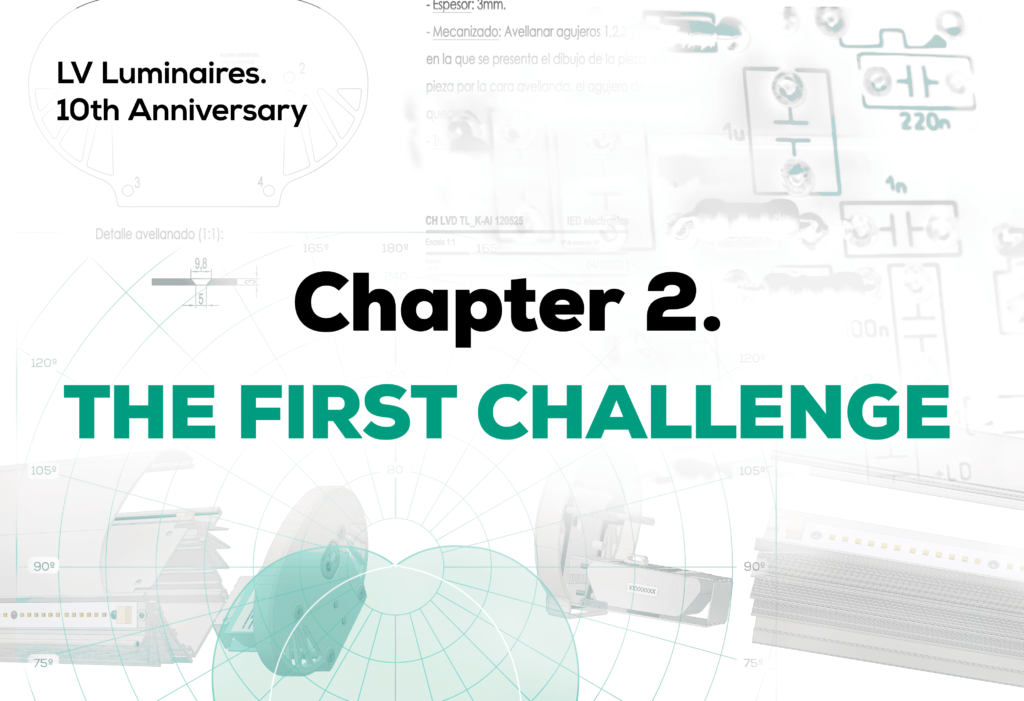
10th anniversary luminaire LV. Chapter 2, ‘The first challenge’
We are in 2013 when our goal of developing the LV luminaire presents three major technical challenges for the IEDGREENPOWER team (which is the name of the company created by Sumelec Grupo and IED Electronics):
– Chemistry Challenge: Battery technology. The wind application is very special, and the majority of batteries are developed for very different applications. These are applications where charge/discharge cycles are often numerous, thermal ranges are controlled, and energy density and speeds are critical… There is a lot of literature and many technologies around this type of performance, but little information and no focus on other much more critical parameters for our luminaire, such as the evolution of the battery capacity over time (in 2013 there is talk of 20 years of life for wind turbines) or in different thermal ranges (there are luminaires in the nacelle and in the tower, in Finland and in Egypt). Of course, we know that the batteries of the luminaires are the cause of many maintenance actions in the field, as well as generating a lot of waste.
So we have to learn a lot about chemistry and batteries, in general, to understand how through our electronics, and by selecting the right chemistry, we can achieve battery lifetimes 3-4 times longer than previous products.
– Train Challenge: Vibrations. Current luminaires are very large (fluorescent size) and plastic. Their dimensions do not help. Neither is useful in the design of fluorescent lamps, elements designed for industrial warehouses, or the residential sector that vibrate much less than the hub of a wind turbine… This is a point to improve because many luminaires or fluorescent lamps are rejected at the installation stage due to transport conditions and in the first months of their life in operation. High cost and a lot of waste.
We have a problem: how to measure if the product we develop is good enough? There are no requirements and no ways to objectively measure the vibration resistance of the product. For other aspects, there were reference tests in the industry, but this could depend on many factors and the requirements are not clear.
What do we do with such a problem? To look at the industry benchmark for vibration, the railway industry, and make an approximation. If it works for a train, it will work for a wind turbine. This is how we validate the vibration behavior.
– A small luxury/s: LEDs. Nowadays few things sound more “common” than LEDs. They are present in many applications. But more than 10 years ago LEDs were very promising products but with two fundamental problems: their efficiency (and their heating) was much lower than it is today and their cost was, on the other hand, much higher. LEDs at that time made the product more expensive than fluorescents and this was a problem as the price pressure was as always huge. But we “believed” in how LED technology would evolve. In addition, the “green” discourse that went with LEDs, we understood that it fitted very well with the sector and with IED’s identity. And the reality is that technically we “wanted to believe” because fluorescent was a brake on the resolution of various problems that the luminaires were causing. Solving them with fluorescent would have been much more complicated and polluting and, over time, would have been much more expensive.
So despite its price, we went for LED from the start… Indeed the technology evolved as we all know and the initial disadvantages would soon be mitigated until they disappeared.
In the next chapter… “Electronics playing thermodynamics”.